I find harddrive docking stations too bulky, slow, and unreliable. They are (1) inconvenient to carry when travelling light with a laptop, (2) offer relatively little throughput because the USB ones are limited to 480Mbps and the eSATA ones are often internally bottlenecked to 1.5Gbps due to the bridge chips they use (nevermind that none support SATA 6Gbps), and (3) are not reliable/act in strange ways when a drive is failing, which is sometimes the reason I put the drive in a docking station —to investigate it— and I wonder if it is the station or the drive that is failing.
Therefore I felt compelled to design and build a coin-sized SATA power module able to power a drive while the latter can be directly connected to a computer via a plain SATA or eSATA cable. I have used it for a couple of days and am very happy with it. Compared to a docking station, my solution is smaller, cheaper, faster, more reliable, and allows connecting any SATA peripherals (optical disc drives, SATA port multipliers):
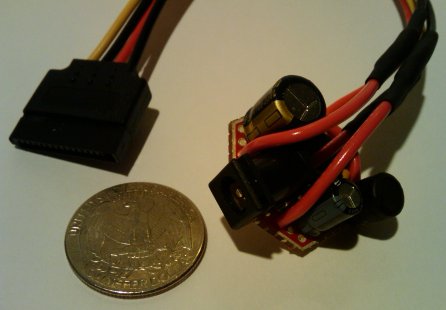
Total cost and time involved were about 9 USD and one afternoon. The power module is compatible with any 12V wall adapter, as long as its current rating is sufficient for the drive —personally I use the 2A-rated adapter from the docking station it replaced :-) It steps down 12V to 5V, and supplies both voltages to the drive:
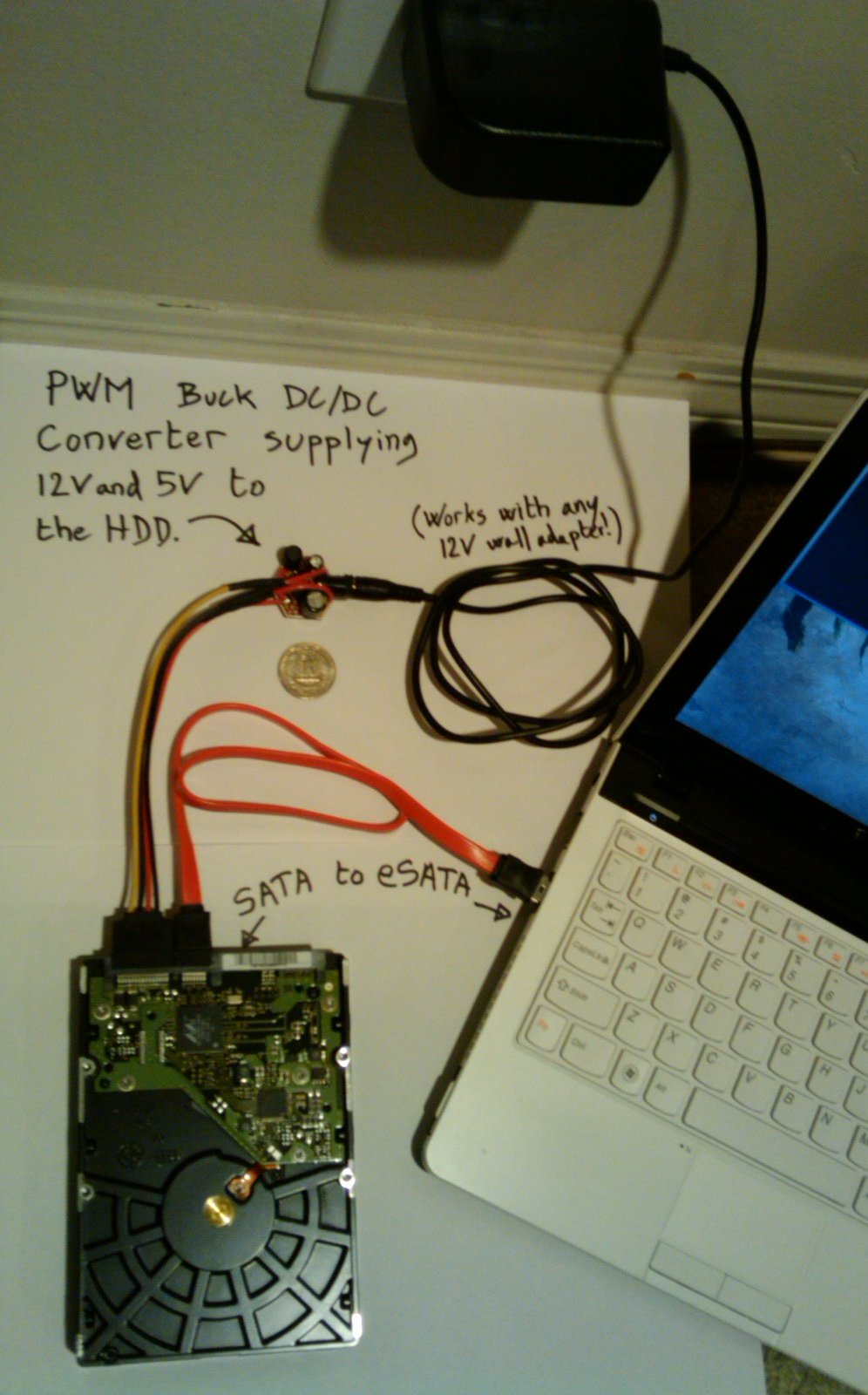
Design
Before I started this project, I knew that a SATA power cable theoretically supplies 3 voltages: 3.3V, 5V, and 12V, but that no drive on the market uses/needs 3.3V. I started by disassembling my Rosewill RX-DUS100 docking station to reverse-engineer the design and find how it was supplying 12V and 5V to the drive. 12V came directly from the output of the wall adapter whereas 5V came from the output of a chip labelled Techcode TD1509 which I quickly found out was, with 2 capacitors, a diode, and an inductor nearby, forming a circuit called a PWM buck DC/DC converter.
I must ashamedly admit I had never heard of buck converters before (hey, electronics is a hobby I rarely practice!) Now armed with the key piece of information I needed, I decided my plan will be to re-use the 12V wall adapter from the docking station, and to build a buck converter on a PCB as small as possible with a DC power jack as the input and a SATA power cable as the output.
I measured the current draw at 12V and 5V on a handful of harddrives and cross-checked with the HDD vendors' datasheets. Drives are never rated more than about 2.5A @ 12V and 0.7A @ 5V. In practice my measurements showed no more than 1.5A @ 12V and 0.6A @ 5V. Power consumption on the 5V rail is pretty much constant, whereas 12V spikes to ~1.5A during spin-up then falls back to ~0.5A. As to my docking station, its 12V wall adapter is rated 2A, and its Techcode TD1509 converter is rated 2A @ 5V (overspec'd because it powers a few other chips in addition to the drive.) With these number in mind, I decided to design my converter for minimum 1A @ 5V.
I searched around on Octopart, Digikey, and found many 5V buck converters. I reduced my search criteria to the high-efficiency, through-hole ones requiring few external components that were inexpensive. I settled on the Nat Semi LM2675, a 1A, DIP8 package, DC/DC converter to 5V. I implemented the reference circuit from the datasheet, and selected external components to match my design specifications (12V input, 1A @ 5V output.) Full bill of materials:
- $0.95 - Sparkfun ProtoBoard, hex shape. Sparkfun is the only vendor I ever found who offers sub $1 prototyping boards with about this amount of board space. If you know others, please share links. This board is not quite the standard 0.1" hole pitch PCB, but all odd and all even rows independently follow this pitch so that it is possible to solder DIP8 packages.
- $0.80 - 2.1mm power jack connector, through-hole, narrow pins. The narrow pins allow it to be soldered on a 0.1" PCB when bent a little. 2.1mm makes it compatible with most docking station wall adapters. The other common inner diameter is 2.5mm.
- $4.48 - National Semiconductor LM2675N-5.0.
- $0.32 - .01uF ceramic capacitor. Used as the boost capacitor.
- $1.13 - 39uH inductor, 1.5A.
- $0.54 - 220uF aluminum capacitor. Used as the output capacitor.
- $0.30 - 100uF aluminum capacitor. Used as the input capacitor.
- $0.54 - 20V 1A Schottky diode.
I found a layout that works well with this PCB, while minimizing the length of certain traces (eg. the Schottky diode needs to be as close to the LM2675 as possible):
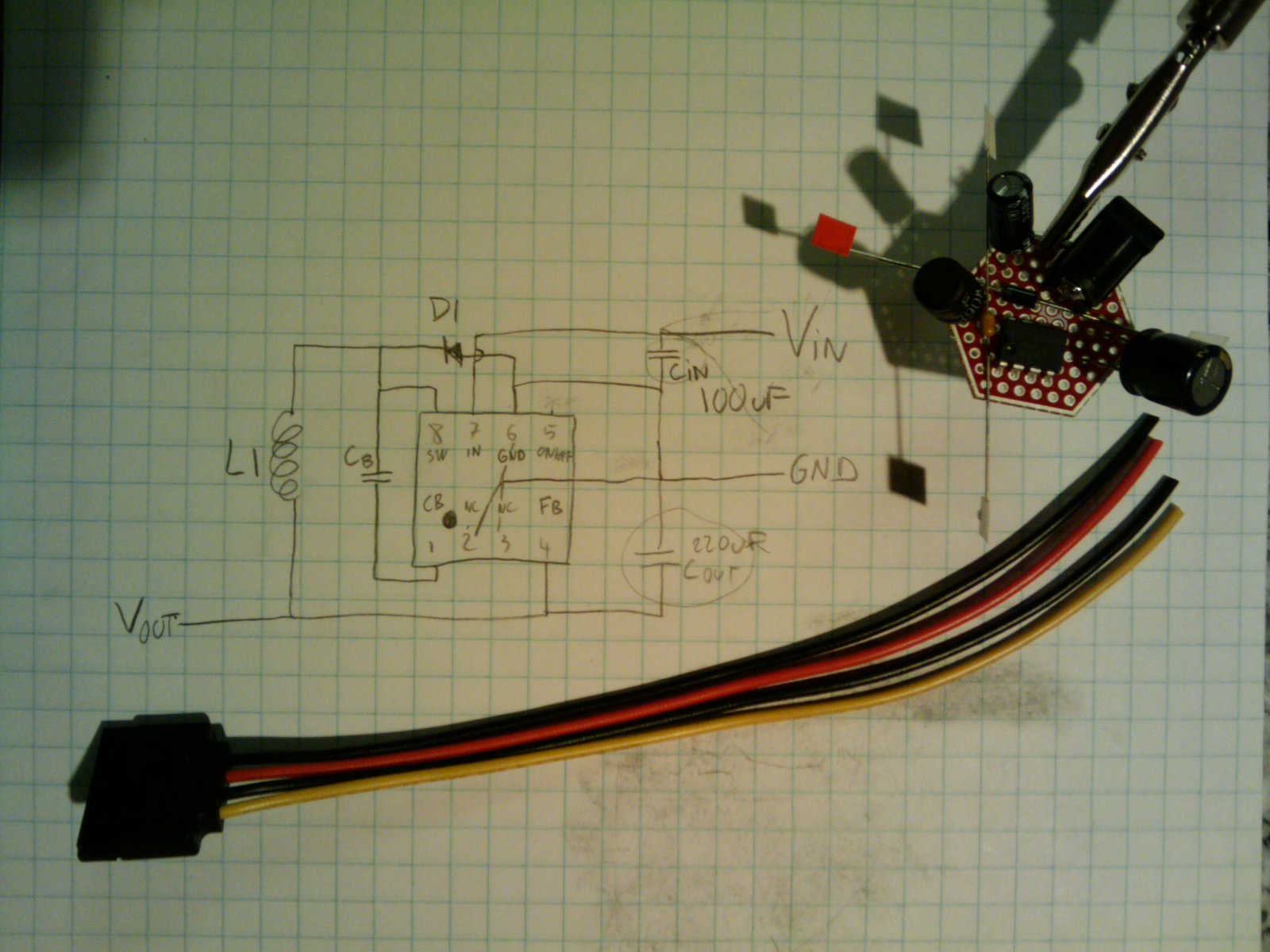
Finally I put some heat-shrink tubing to finish the product:
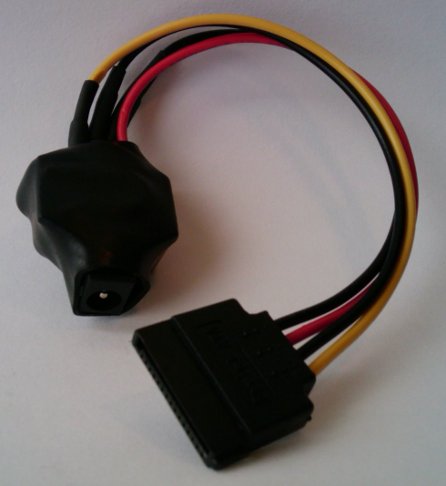
Possible Improvement
The current design requires a 12V wall adapter because this 12V input is output directly to the drive. One could add another DC/DC conversion step (at the cost of increased board size) to regulate 12V, thereby making the SATA power module compatible with a wider range of input voltages, such as a laptop power adapter. One less adapter to travel with!
I would be very happy to see a commercial product like mine. I found only one on Newegg but it is still too bulky and clumsy to my taste (separate thick IEC power cord, brick adapter, 4-pin molex power cable, 4-pin molex to SATA power adapter).